As one of Ireland’s leading vacuum forming specialists, Donite Plastics has nearly 40 years of experience in the industry. We are experts in using vacuum forming to make plastic parts that are durable, attractive and cost-effective.
Working for Donite Plastics means that I’ve been asked a question or two about vacuum forming in my time, so I decided to pull together a little Q&A for anyone who is still curious.
Q. What does thermoforming and vacuum forming mean?
A. Thermoforming is a plastic moulding process where a sheet of plastic is heated to a high temperature and then formed over a mould. Vacuum forming is the specific thermoforming process where a vacuum is used to force/pull the heated plastic into the shape of the mould. Once the plastic has taken the shape of the mould it is then trimmed to be used as a product.
The process starts with our design team, who create a design using the latest computer technology (CAM) to produce CNC programmes based on CAD models. These programmes are then used to make the moulds and to trim the moulded parts. Our dedicated staff have many years of experience and work closely with our customers throughout the entire process to ensure their product is of the highest standard.
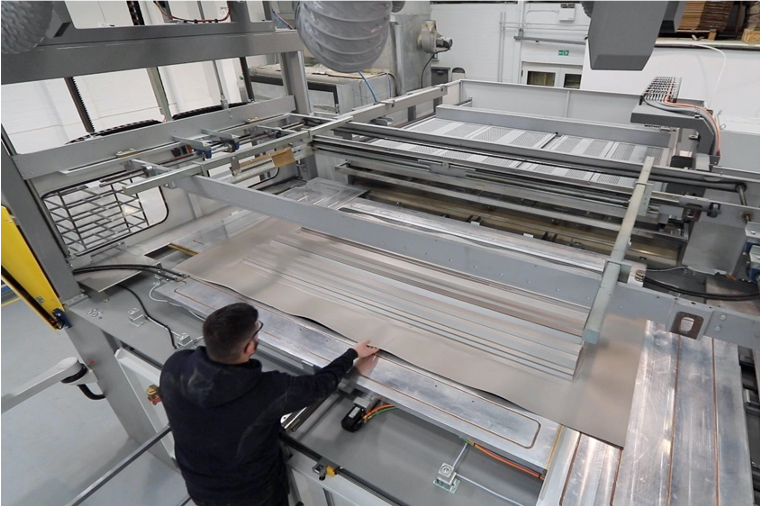
These programmes are then used to make the moulds and to trim the moulded parts. Our dedicated staff have many years of experience and work closely with our customers throughout the entire process to ensure their product is of the highest standard.
Q. What products would thermoforming be suitable for?
A. Thermoforming is suitable for producing a wide range of plastic parts in many shapes and sizes and offers many advantages over other plastics processing methods. At Donite Plastics we produce parts that are a variety of sizes – we can make parts from a few centimetres in size to parts that are 2.5 x 1.5 metres x 0.8 metres high.
When I mention vacuum forming or thermoforming, people often think of lightweight packaging. However, using vacuum forming processes, we only make heavy-duty industrial mouldings as opposed to lightweight packaging.
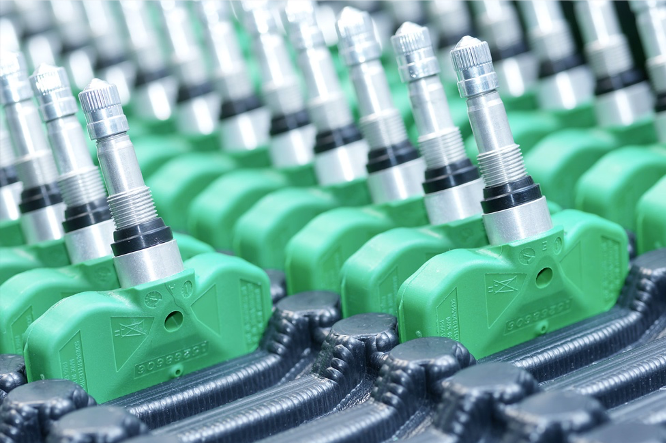
Q. What types of industries require thermoformed products?
A. We service many sectors at Donite Plastics; at the time of writing, we have manufactured over 100,000 thermoformed parts for a leading aircraft interior company. Our experienced design team work with our customers to develop unique solutions to enhance their product. This might be specially moulded trays used to transport parts down a production line, a new enclosure for an electronic or medical device or a large panel for a piece of agricultural machinery.
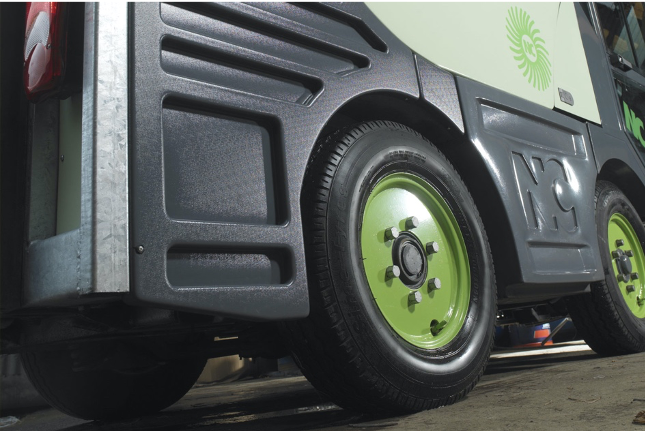
What are the design benefits of vacuum forming?
A. Choosing thermoformed plastic products over other plastic forming methods such as injection moulding has its benefits. What customers really love about thermoforming are the low costs and the fast turnaround times to production. In a marketplace dominated by brands and logos, the design flexibility of vacuum formed products is another advantage. By using moulds, vacuum forming allows product designers to realise the design aesthetics of their company.
Q. What kind of cosmetic features does vacuum forming allow?
A. As vacuum forming is flexible and adaptable to the customer’s design needs, there are many different cosmetic features that can be made. You can form incredibly detailed and sharp shapes, logos, text, with a wide variety of coloured and paintable plastics.
Michael Barton